Unveiling the Power of Injection Plastic Molding: The Ultimate Guide for Industry Leaders
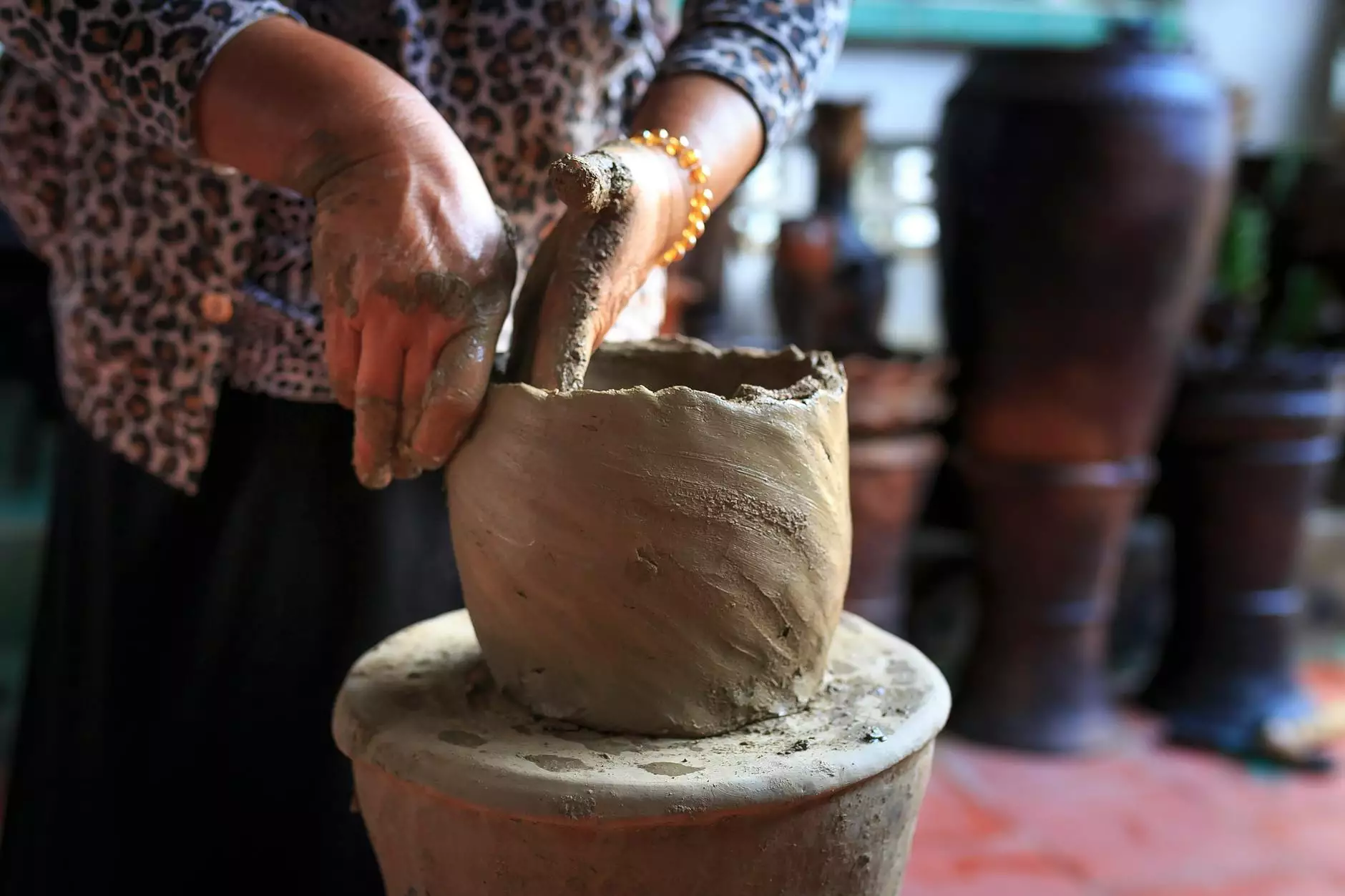
In today’s fast-paced manufacturing landscape, the importance of innovative and efficient production techniques cannot be overstated. Among these, injection plastic molding stands out as a cornerstone process revolutionizing the way complex plastic components are produced with precision, speed, and cost-efficiency. As a premier Metal Fabricator at DeepMould.net, we are committed to delivering unparalleled expertise and advanced solutions tailored for diverse industrial applications.
Understanding the Fundamentals of Injection Plastic Molding
Injection plastic molding is an advanced manufacturing process that involves injecting molten plastic material into a meticulously designed mold cavity. Once cooled and solidified, this process yields high-precision, durable plastic parts suitable for various industries, including automotive, consumer electronics, medical devices, and packaging.
This method is celebrated for its ability to produce complex geometries with tight tolerances, minimizing material waste and reducing post-processing requirements. The process typically involves several key stages:
- Design & Mold Fabrication: Creating a detailed mold that defines the shape and features of the final product.
- Material Preparation: Choosing the right thermoplastic resin aligned with product specifications.
- Injection & Cooling: Melting the thermoplastic resin and injecting it under high pressure into the mold cavity, followed by cooling to form the part.
- Ejection & Finishing: Removing the finished component and performing any necessary finishing touches.
The Significance of Advanced Injection Plastic Molding in Modern Manufacturing
Today, injection plastic molding is fundamental for producing consistent, high-quality plastic components at scale. Its significance stems from several key advantages:
- High Precision and Reproducibility: Capable of producing complex intricate parts with minimal variations.
- Cost-Effectiveness: Reduces labor and material costs through automation and efficient use of raw materials.
- Rapid Production Cycles: Enables mass production, matching the demands of high-volume manufacturing.
- Design Flexibility: Facilitates the creation of complex geometries, including undercuts, threads, and textured surfaces.
- Material Versatility: Supports an extensive range of thermoplastics and thermosetting plastics to suit various performance needs.
Why DeepMould.net Is Your Trusted Partner for Metal Fabrication and Injection Molding Solutions
At DeepMould.net, we have established ourselves as a leader in personalized metal fabrication and integrated injection plastic molding services that guarantee excellence from concept to completion. Our extensive experience in the industry, state-of-the-art machinery, and dedicated team of specialists enable us to deliver products that surpass customer expectations.
Our Comprehensive Capabilities in Injection Plastic Molding
We offer a full range of services aligned with the highest industry standards, including:
- Design for Manufacturing (DFM): Collaborating with clients to optimize product designs for manufacturability and cost savings.
- Prototype Development: Rapid prototyping to validate designs and reduce time-to-market.
- Tooling & Mold Fabrication: Precision machining and high-quality mold manufacturing to ensure tight tolerances.
- Mass Production: Large-scale manufacturing with strict quality control protocols.
- Material Selection & Testing: Expert guidance on choosing the right plastics and conducting thorough testing for durability and performance.
The Role of Precision Engineering in Injection Plastic Molding
A core element of our success and the key to outperforming competitors in injection molding lies in our commitment to precision engineering. We utilize advanced computer-aided design (CAD) and computer-aided manufacturing (CAM) systems for mold design and analysis, ensuring that every component meets exact specifications.
Our facilities are equipped with high-end CNC machines and molding presses ranging from small-scale prototypes to large industrial units. This range allows us to handle projects of all sizes with exceptional accuracy and consistency. Precise temperature and pressure controls, combined with real-time process monitoring, allow us to optimize each molding cycle, resulting in top-tier quality parts with minimal rejects.
Innovations Driving the Future of Injection Plastic Molding
As industry leaders, we continuously explore and implement innovations that push the boundaries of what is possible with injection plastic molding. Some of these advancements include:
- Smart Molds: Incorporating sensors for real-time feedback, enabling adaptive process control.
- Eco-Friendly Materials: Developing and utilizing biodegradable and recyclable plastics to meet sustainability goals.
- Automation and Robotics: Streamlining production lines to enhance efficiency and reduce human error.
- 3D-Printed Molds: Utilizing additive manufacturing for rapid mold prototyping and small batch production.
- Micro Molding: Creating miniature components for high-tech applications, including medical devices and electronics.
Quality Assurance & Certification in Injection Molding
Maintaining consistent quality is paramount in production. At DeepMould.net, we integrate rigorous quality assurance protocols into every step of our injection plastic molding process. Our facilities are ISO 9001 certified, ensuring adherence to international standards.
We conduct comprehensive inspections, including dimensional analysis, material testing, and durability assessments, to verify that every batch meets specifications. Our use of advanced inspection equipment such as coordinate measuring machines (CMM) and ultrasonic testing devices guarantees accuracy and reliability, providing peace of mind to our clients.
Custom Solutions Tailored to Your Industry Needs
Whether you require complex medical implants, high-performance automotive components, or consumer product housings, our bespoke injection plastic molding services are designed to meet unique industry standards and technical specifications. We work closely with you through every phase — from initial concept to final delivery — ensuring your visions are realized with precision and efficiency.
Advantages of Partnering with DeepMould.net for Your Injection Molding Needs
Choosing DeepMould.net translates into tangible benefits:
- Unmatched Quality: Superior craftsmanship and rigorous quality controls.
- Technical Expertise: Experienced engineers proficient in complex mold designs and material science.
- Cost Optimization: Competitive pricing through efficient processes and bulk production capabilities.
- Fast Turnaround: Accelerated project timelines without compromising quality.
- End-to-End Service: From design and prototyping to mass production and logistics support.
Investing in the Future: Sustainability and Innovation in Injection Molding
As sustainability becomes a driving force in manufacturing, we are dedicated to integrating eco-conscious practices into our injection plastic molding processes. This includes adopting recyclable plastics, reducing energy consumption through optimized processes, and developing environmentally friendly mold designs.
Furthermore, our ongoing investment in cutting-edge technology and research ensures that our clients stay ahead in competitive markets, benefiting from innovations such as bioplastics, micro-injection molding, and smart manufacturing systems.
Conclusion: Your Success with DeepMould.net
In the realm of metal fabricators and top-tier injection plastic molding providers, DeepMould.net stands as a symbol of excellence, precision, and innovation. Our comprehensive services, advanced technology, and unwavering commitment to quality create an unmatched platform for realizing your manufacturing ambitions.
Partner with us to harness the full potential of injection plastic molding and elevate your products to new heights of performance and reliability. Your success is our mission, and at DeepMould.net, we turn your ideas into innovative, durable, and cost-effective solutions that define the future of manufacturing.