Ultimate Guide to Pressure Vessel Inspection for Safe and Efficient Business Operations
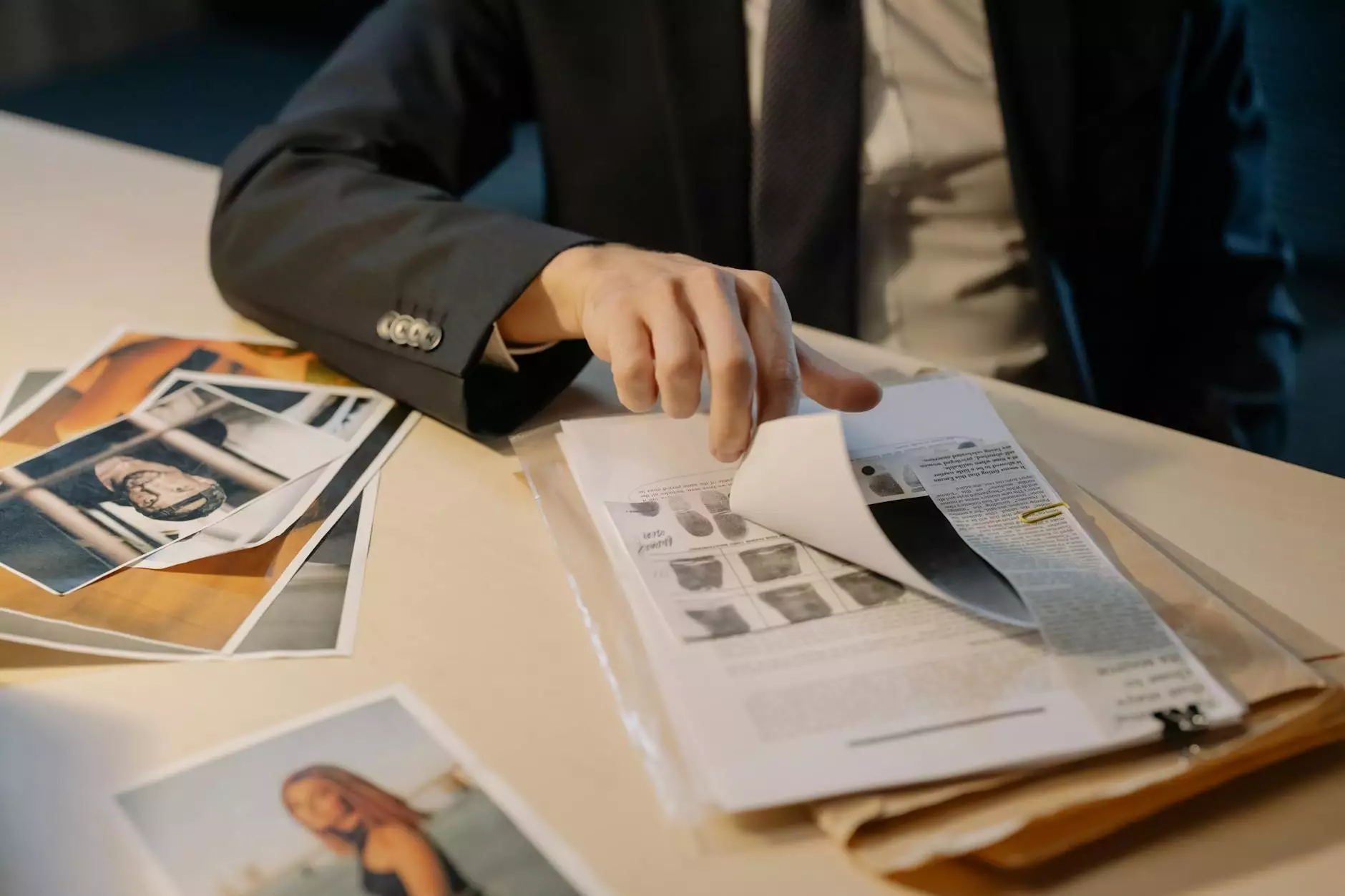
In today’s rapidly evolving industrial landscape, the safety, reliability, and performance of equipment are paramount. Among the critical components in many manufacturing, chemical, and energy sectors are pressure vessels, which contain gases or liquids under high pressure. Ensuring their integrity through rigorous pressure vessel inspection is essential not only for regulatory compliance but also for safeguarding personnel, protecting assets, and maintaining seamless operations. This comprehensive guide delves into the core aspects of pressure vessel inspection, emphasizing its significance, methodologies, and best practices tailored specifically for businesses operating within the domains of Home & Garden, Gardeners, and Pest Control sectors, as well as broader industrial applications.
Understanding the Significance of Pressure Vessel Inspection
Pressure vessels are used extensively in various industries to hold gases or liquids at elevated pressures. From storage tanks to process reactors, their role is critical but also inherently risky if not properly maintained. An uninspected or poorly maintained pressure vessel can lead to catastrophic failures, resulting in injuries, environmental damage, and significant financial losses.
Therefore, pressure vessel inspection is an indispensable part of preventative maintenance. It ensures that the containers are functioning within safe parameters, detects early signs of deterioration such as corrosion, fatigue, or material degradation, and verifies compliance with safety standards dictated by relevant authorities such as the Pressure Equipment Directive (PED) and ASME codes.
Legal and Safety Framework Surrounding Pressure Vessel Inspection
Adherence to legal safety standards is not optional. Businesses must comply with regulations including:
- Pressurized Equipment Directive (PED): Ensures safety and conformity for pressure equipment within the European Union.
- ASME Boiler & Pressure Vessel Code: Sets standards for design, fabrication, testing, and inspection in North America.
- UK Pressure Systems Safety Regulations (PSSR): Mandate routine checks for safety compliance in the United Kingdom.
Regular pressure vessel inspection activities are mandated by these frameworks, requiring qualified inspectors to assess integrity and certify that vessels are safe for continued operation.
Types of Pressure Vessel Inspection: A Deep Dive
Comprehensive pressure vessel inspection comprises several methodologies aimed at early detection of faults, ensuring operational safety, and extending equipment lifespan. The main types include:
Visual Inspection (VI)
The most basic and fundamental form of inspection, involving a thorough visual assessment of the vessel's external and accessible internal surfaces. Inspectors look for signs of corrosion, cracks, dents, leaks, or weld defects. Visual inspection can often be supplemented with magnification tools and cameras to identify flaws not visible to the naked eye.
Non-Destructive Testing (NDT)
NDT methods are crucial for evaluating the internal condition of pressure vessels without causing damage. Key NDT techniques include:
- Ultrasonic Testing (UT): Utilizes high-frequency sound waves to detect internal flaws, thin spots, or corrosion.
- Radiographic Testing (RT): Employs X-ray or gamma-ray imaging to identify internal cracks or manufacturing defects.
- Magnetic Particle Testing (MPT): Detects surface and near-surface discontinuities in ferromagnetic materials.
- Liquid Penetrant Testing (LPT): Highlights surface-breaking defects to assess weld quality.
- Eddy Current Testing (ECT): Used mainly on metallic surfaces to identify corrosion or cracking phenomena.
Pressure and Leak Testing
Once physical inspection and NDT validation are performed, vessels often undergo pressure testing—either hydrostatic or pneumatic—to ensure they can withstand operational pressures without failure or leaks.
Critical Factors and Best Practices for Successful Pressure Vessel Inspection
Implementing best practices enhances the accuracy and effectiveness of inspections, ultimately improving safety standards and operational efficiency. Key aspects include:
- Schedule and Frequency: Regular inspections aligned with manufacturer guidelines, industry standards, and operational cycles.
- Qualified Personnel: Employ experienced and certified inspectors with expertise in pressure vessel codes and standards.
- Documentation and Records: Maintain meticulous records of inspection findings, repairs, and modifications for regulatory audits and future reference.
- Use of Advanced Technologies: Incorporate cutting-edge tools such as digital radiography, ultrasonic thickness gauges, and drone-based inspection for inaccessible areas.
- Corrosion Management: Regularly assess corrosion rates and implement mitigation strategies such as coatings or cathodic protection.
- Repair and Maintenance: Address defects promptly with qualified welding or material replacement procedures to prevent escalation.
The Role of Pressure Vessel Inspection in Business Continuity and Cost Efficiency
Investing in rigorous pressure vessel inspection protocols offers tangible benefits beyond safety:
- Reduced Downtime: Early fault detection prevents unexpected failures that could halt operations.
- Extended Equipment Lifespan: Regular maintenance and timely repairs prolong the service life of pressure vessels.
- Cost Savings: Prevents expensive emergency repairs and mitigates costs associated with accidents or environmental compliance violations.
- Enhanced Reputation: Demonstrating commitment to safety and quality boosts client confidence and brand integrity.
Special Considerations for Businesses in Home & Garden, Gardeners, and Pest Control Sectors
While pressure vessel inspection might seem more prevalent in industrial settings, businesses in the Home & Garden, Gardeners, and Pest Control sectors that utilize portable tanks, compressed gas cylinders, or chemical containers must also adhere to safety standards. Proper inspection ensures:
- Preventing leaks of hazardous chemicals or gases.
- Maintaining compliance with environmental regulations.
- Ensuring safety procedures for personnel handling pressurized equipment.
- Protection of consumers and the environment from accidental releases.
Partnering with Experts: Why Choose Safe Plant UK for Pressure Vessel Inspection
At Safe Plant UK, we specialize in comprehensive inspection services tailored to your specific industry needs. Our team of certified inspectors utilizes state-of-the-art technology and adheres strictly to regulatory standards, ensuring your pressure vessels are safe, compliant, and performing optimally.
Additionally, our services include:
- Routine inspection scheduling and documentation
- Advanced non-destructive testing techniques
- Detailed reporting and expert recommendations
- Assistance with repairs, maintenance, and certification processes
Conclusion: Prioritize Safety with Expert Pressure Vessel Inspection
In the realm of business operations that involve pressurized equipment, pressure vessel inspection is not merely a regulatory requirement—it is a crucial element of risk management and operational excellence. Regular inspections, carried out by qualified professionals using advanced techniques, serve as an effective safeguard against accidents, optimize asset performance, and underpin sustainable business growth.
As leaders in the industry, Safe Plant UK is committed to helping your business uphold the highest safety standards. Whether you operate within Home & Garden, Gardeners, Pest Control, or broader industrial sectors, trust us to deliver reliable, expert pressure vessel inspection solutions that keep your operations safe, compliant, and efficient.
Contact us today to learn more about how our inspection services can benefit your organization and ensure the integrity of your pressurized equipment.