The Importance of Phosphating Plants in Automotive Manufacturing
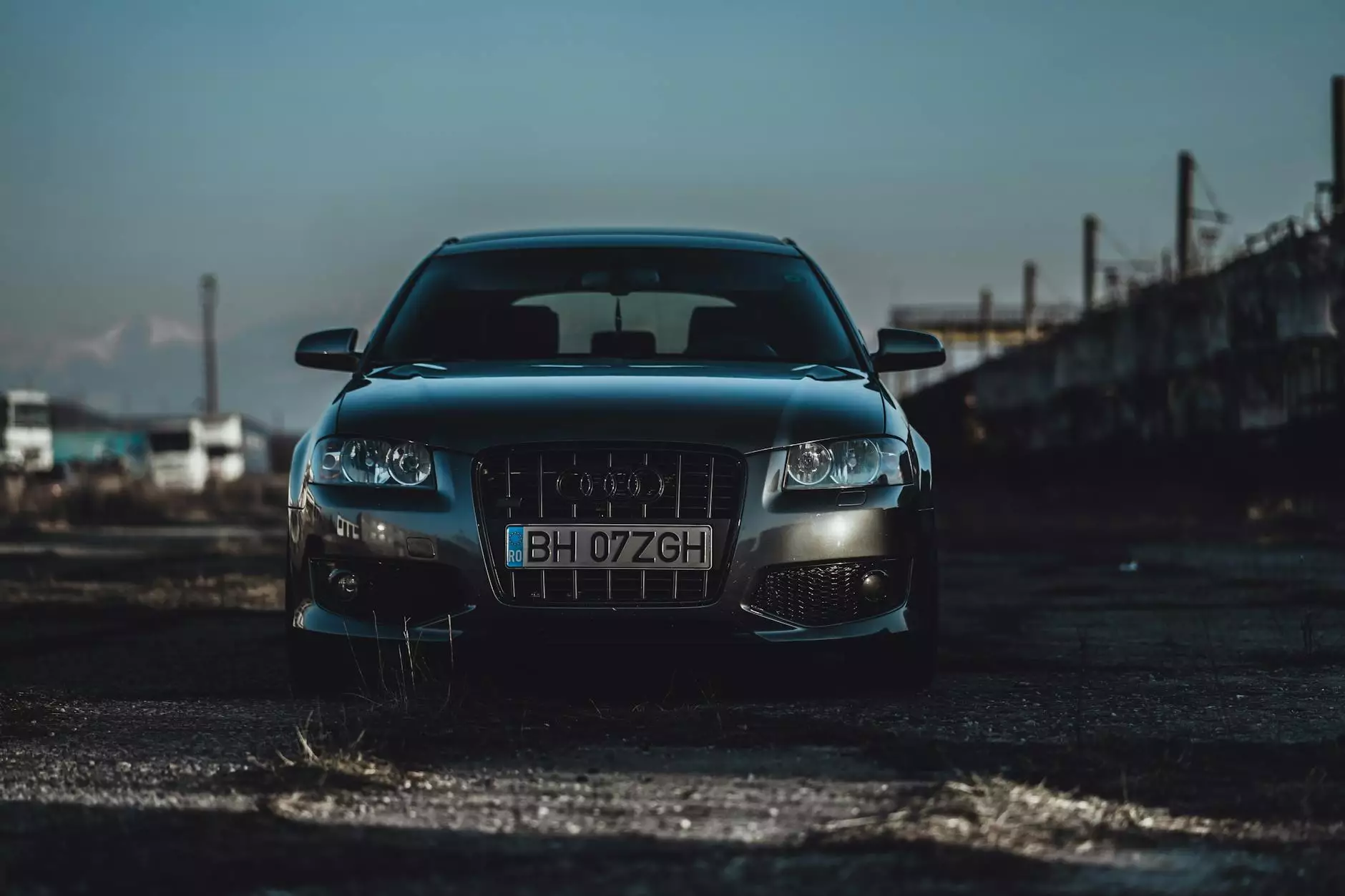
In the modern automotive industry, maintaining high standards of quality and durability is crucial. Phosphating plants play a significant role in achieving these standards by providing essential pre-treatment processes that enhance adhesive bonding, corrosion resistance, and overall performance of metal components. This article delves deep into the world of phosphating plants, their operational mechanisms, and their undeniable impact on the automotive sector.
What is a Phosphating Plant?
A phosphating plant is a dedicated facility that utilizes a chemical process known as phosphating to enhance the properties of metal surfaces. Phosphating involves the application of a phosphate conversion coating to metals, primarily steel and iron, to improve their corrosion resistance and prepare them for further coatings such as paint.
The Phosphating Process Explained
Understanding the phosphating process is key to appreciating its significance in manufacturing. Here are the primary steps involved:
- Cleaning: The first step involves cleaning the metal surface to remove oils, dirt, and any contaminants. This is typically done using alkaline cleaners.
- Rinsing: After cleaning, the surfaces are rinsed with water to eliminate any residual cleaning agents.
- Phosphating: The cleaned metal is submerged in a phosphating solution, which typically contains zinc or manganese phosphates. This step creates a uniform phosphate layer on the metal surface.
- Rinsing Again: A secondary rinse removes any excess phosphating solution.
- Drying: The final step involves drying the coated metal to ensure the phosphate layer adheres properly. This can involve air drying or drying in an oven.
The Benefits of Using Phosphating Plants
Utilizing phosphating plants provides numerous advantages to the automotive manufacturing process:
- Corrosion Resistance: The primary benefit of phosphating is enhanced corrosion protection, which is critical for the longevity of automotive components.
- Improved Adhesion: Phosphate coatings promote better adhesion of subsequent layers like paints or powder coatings, leading to a more durable finish.
- Cost-Effectiveness: Phosphating can be a cost-effective solution as it reduces the need for extensive corrosion protection measures later in the production process.
- Environmentally Friendly: Modern phosphating solutions are designed to be less harmful to the environment, thus adhering to regulatory standards.
- Versatility: Phosphating can be used on a variety of metals and components, making it a versatile choice for manufacturers.
Applications of Phosphating in the Automotive Industry
Phosphating is utilized in various applications within the automotive sector:
- Chassis Components: Enhancing the rust resistance of components like frames, subframes, and brackets.
- Body Panels: Preparing body panels for painting to ensure a smooth, adherent finish.
- Engine Parts: Treatment of engine components to resist wear and corrosion from exposure to heat and chemicals.
- Fasteners: Providing corrosion protection for bolts, nuts, and screws to maintain integrity over time.
Environmental Considerations of Phosphating Plants
As industries shift towards more sustainable practices, phosphating plants are evolving to meet environmental standards:
- Waste Management: Proper treatment and disposal of wastewaters and sludge are essential to minimize environmental impact.
- Use of Eco-Friendly Chemicals: Many phyisical-phosphating processes are adapting to use less hazardous substances and promote sustainability.
- Energy Efficiency: Modern plants are designed to optimize energy use, reducing their carbon footprint.
Investing in Quality Phosphating Plants
Choosing the right phosphating plant is crucial for automotive manufacturers. Here are some factors to consider:
- Technology: Evaluate the technology behind the phosphating plant, ensuring it meets industry standards and provides flexibility in processing different components.
- Capacity: Assess the production capacity to match your manufacturing needs and future growth.
- Support and Maintenance: A reliable manufacturer will offer ongoing support and maintenance services to minimize downtime.
- Cost: While quality is vital, budget considerations must also play a role in the decision-making process.
The Future of Phosphating in Automotive Manufacturing
As technology continues to advance, the future of phosphating in the automotive industry looks promising:
- Innovation: Continuous research into better phosphating solutions and processes can lead to improved results and efficiencies.
- Hybrid Solutions: The combination of phosphating with other finishing technologies, such as nano-coatings, is emerging as a new trend.
- Automation: Increased automation within phosphating plants can enhance efficiency, reduce scrap rates, and improve consistency.
Conclusion
In conclusion, phosphating plants serve as a cornerstone in the automotive manufacturing process. Their ability to enhance corrosion resistance, improve adhesion, and promote longevity makes them indispensable. As the industry evolves, the focus on sustainable practices and innovative technologies ensures that phosphating remains relevant and crucial. Investing in quality phosphating processes not only enhances product performance but also positions manufacturers for success in a competitive market. By embracing these advancements, companies like Autocoat India can continue to lead the charge toward a more effective and environmentally friendly automotive manufacturing sector.
Incorporating high-quality phosphating services into your production lines is not just a trend; it’s a necessity for automotive excellence. As the future unfolds, the integration of phosphating plants will undoubtedly play a significant role in elevating the automotive industry's standards and pushing the boundaries of what’s possible.