The Vital Role of Lathe Machining Parts Manufacturers in Metal Fabrication
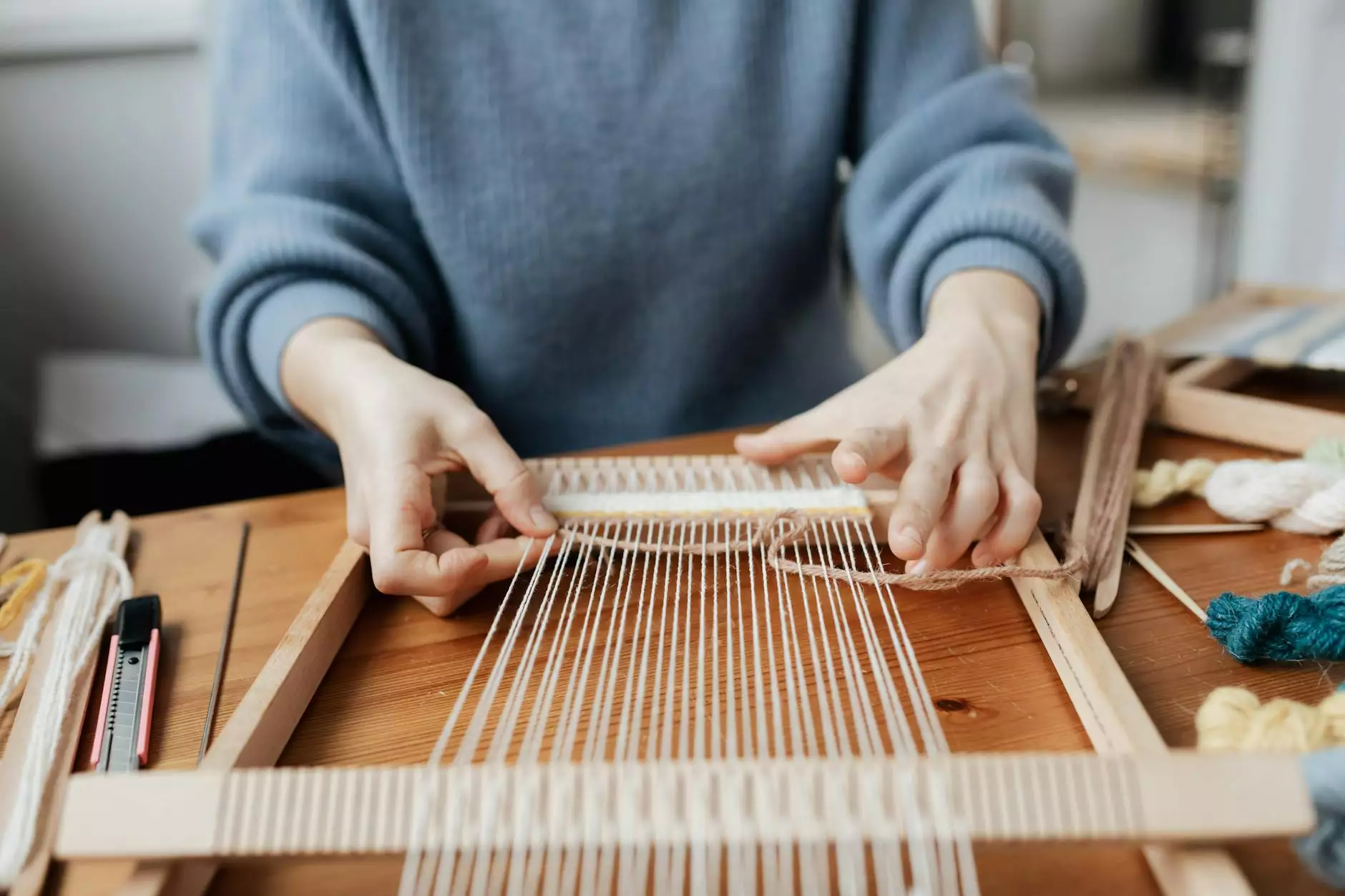
In the ever-evolving landscape of manufacturing, lathe machining parts manufacturers stand out as key players in the realm of metal fabrication. These manufacturers are crucial to myriad industries, generating components that serve as the backbone for various applications, from automotive to aerospace and everything in between. This article delves into the significance of these manufacturers, detailing their processes, contributions, and the future of lathe machining in the industry.
What is Lathe Machining?
Lathe machining is a subtractive manufacturing process where material is removed from a rotating workpiece to create cylindrical or flat surfaces. The key tool in this process is the lathe, which spins the material while a stationary cutting tool removes unwanted material, leading to the desired shape and finish. This precision process allows for high accuracy and repeatability, making it indispensable for manufacturers who require consistent and reliable components.
The Importance of Lathe Machining Parts Manufacturers
The demand for precision-engineered components is rising, with lathe machining parts manufacturers being at the forefront of this trend. They provide various parts such as shafts, bushings, gears, and custom components tailored to specific needs. Here are several key points that emphasize their importance:
- Quality Assurance: Manufacturers emphasize quality at every stage, employing rigorous testing standards to ensure that each component meets industry specifications.
- Customization: Many manufacturers offer tailored solutions to meet the unique requirements of different industries. This ability to customize is critical for applications that require specific dimensions and tolerances.
- Innovation: The integration of advanced technologies such as CNC (Computer Numerical Control) lathes has revolutionized traditional machining, enabling faster production times and improved precision.
- Cost-Effectiveness: High-volume production through lathe machining can significantly reduce costs per unit, making it a financially viable option for many businesses.
Key Processes in Lathe Machining
Understanding the processes utilized by lathe machining parts manufacturers gives insight into the intricacies of metal fabrication. Here are some critical processes:
1. Turning
Turning is the most fundamental aspect of lathe machining. By rotating the material against a cutting tool, manufacturers can create precise diameters, grooves, and threads on the workpiece. This process can yield components with a high level of circular accuracy.
2. Drilling
Coupling lathe machines with drilling tools allows manufacturers to create holes in the workpiece. This is essential for creating parts that will fit into assemblies, ensuring that different components can be integrated smoothly.
3. Boring
Boring is used to expand existing holes to a precise diameter. This process ensures that holes meet strict tolerance requirements, which is crucial in applications where fit and alignment are critical.
Benefits of Working with Lathe Machining Parts Manufacturers
Businesses benefit tremendously from collaborating with professional lathe machining parts manufacturers. Here are some notable advantages:
- Expert Knowledge: These manufacturers possess extensive industry knowledge, enabling them to provide valuable insights into material selection, design optimization, and cost-saving strategies.
- Advanced Technology: Manufacturers invest in cutting-edge technology and machinery. This commitment ensures that businesses receive high-quality components manufactured with the best processes.
- Reliability: Partnering with reputable manufacturers means businesses can rely on timely delivery and consistent quality, allowing for uninterrupted production lines.
- Sustainability: Many modern manufacturers focus on sustainable practices, using recyclable materials and efficient processes to minimize waste and energy consumption.
Choosing the Right Lathe Machining Parts Manufacturer
When selecting a lathe machining parts manufacturer, there are several factors to consider to ensure you choose a partner who aligns with your business needs:
1. Experience and Reputation
Investigating a manufacturer's experience and industry reputation is essential. A manufacturer with a solid track record is more likely to deliver superior products and services.
2. Capability and Technology
Understanding the technological capabilities of the manufacturer is crucial. Ensure they have the necessary equipment to handle your specific machining requirements and can produce parts within your desired tolerances.
3. Certification and Compliance
Always check for relevant certifications (such as ISO 9001) which indicate that the manufacturer adheres to industry quality standards. Compliance with these standards ensures that you are partnering with a competent manufacturer.
Applications of Lathe Machined Parts
The parts produced by lathe machining parts manufacturers find their way into various sectors. Some of the notable applications include:
- Automotive Industry: Components such as axles, shafts, and pump housings are machined to precise specifications for optimized performance.
- Aerospace Industry: Parts must meet rigorous standards; therefore, precision and reliability are paramount in components such as landing gear and engine parts.
- Medical Devices: Custom-crafted components are essential in medical devices, where precision can be a matter of life and death.
- Industrial Machinery: Lathe machined parts form the components of industrial machinery, ensuring efficient operation across various manufacturing processes.
The Future of Lathe Machining
As industries continue to evolve, so too does lathe machining. The future holds exciting prospects for lathe machining parts manufacturers, particularly in the integration of new technologies:
1. Automation
The introduction of automation in machining processes is set to enhance productivity and reduce labor costs, allowing for faster turnaround times without compromising quality.
2. Industry 4.0
The shift towards Industry 4.0 emphasizes interconnected devices and smart manufacturing. Lathe machining will increasingly integrate IoT (Internet of Things) technologies, allowing real-time monitoring and predictive maintenance.
3. Material Advancements
Advances in material science will enable the production of new alloys and composite materials that may provide improved performance characteristics for machined parts.
Conclusion
In conclusion, the role of lathe machining parts manufacturers in the metal fabrication industry cannot be overstated. Their expertise, innovative practices, and commitment to quality are instrumental in driving progress across various sectors. Businesses looking for precision-engineered components must carefully select their manufacturing partners, ensuring they align with industry standards and demonstrate a commitment to excellence.
As we look to the future, the integration of advanced technologies and sustainable practices will shape the trajectory of lathe machining, making it an exciting field with boundless opportunities for both manufacturers and their clients. By understanding and leveraging the advantages offered by lathe machining, businesses can position themselves at the forefront of competitiveness in the ever-demanding market landscape.