The Essential Role of an Injection Mould Maker in Modern Manufacturing
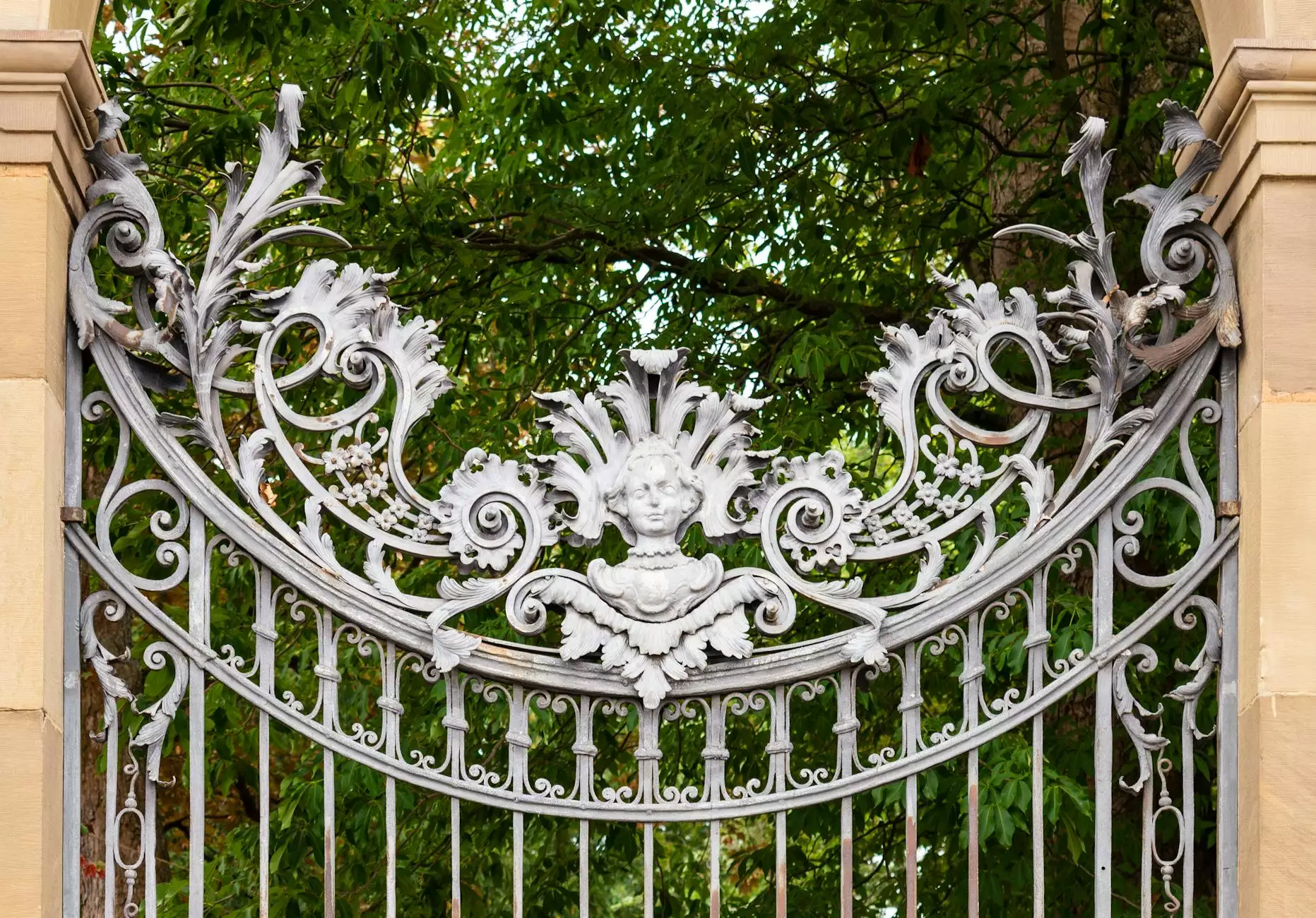
In today's competitive market, businesses rely heavily on efficient manufacturing processes to stay ahead. One of the most critical components of this process is the role of the injection mould maker. These professionals are tasked with crafting the tools that produce high-quality plastic parts efficiently and cost-effectively. In this article, we will delve into the significance of choosing the right injection mould maker, the processes involved, and how it impacts your business's bottom line.
Understanding the Injection Moulding Process
Injection moulding is a manufacturing process where molten plastic is injected into a mould to create various products. This method is widely used for producing plastic components in industries ranging from automotive to consumer goods. To ensure consistency and quality in production, a proficient injection mould maker is indispensable.
The Components of the Injection Moulding Process
- Material Selection: Choosing the right type of plastic for your application.
- Mould Design: Creating a precise and efficient mould that meets design specifications.
- Injection: Heating the plastic and injecting it into the mould at high pressure.
- Cooling: Allowing the moulded part to cool and solidify before removal.
- Finishing: Post-processing steps to ensure the final product meets quality standards.
Why Choosing the Right Injection Mould Maker Matters
The success of your production line hinges on the capabilities of your injection mould maker. Working with a reputable and experienced mould manufacturer can streamline the production process, reduce costs, and improve the quality of the end product. Let's explore several factors that highlight the importance of this choice:
1. Expertise and Experience
Experienced injection mould makers possess industry knowledge that can help avoid common pitfalls during the design and manufacturing process. They can provide insights into:
- Material properties and how they affect design choices.
- Best practices for achieving tight tolerances and complex geometries.
- Recommendations on optimizations that save time and costs.
2. Quality Assurance
Quality is paramount in production. A reliable injection mould maker implements rigorous quality control processes. This can include:
- Regular inspections during the mould manufacturing process.
- Testing prototypes to ensure they meet specifications.
- Continuous feedback loops for process improvement.
3. Technology and Innovation
The landscape of manufacturing is changing rapidly due to advancements in technology. A skilled injection mould maker will stay abreast of the latest technologies and methodologies, such as:
- 3D printing for rapid prototyping.
- Advanced simulation software for mould flow analysis.
- Integration of automation in manufacturing processes.
4. Cost-Effectiveness
Investing in a high-quality mould might seem costly upfront; however, it ensures better durability and less maintenance over time. A proficient injection mould maker can help optimize the design to minimize production costs.
Cost Benefits Include:
- Reduced cycle times leading to higher output.
- Fewer defects, leading to lower waste and rework costs.
- Longer-lasting moulds that require less frequent replacement.
Choosing the Right Plastic Mold Maker
Selecting a top-tier plastic mold maker is a critical decision that will impact your manufacturing journey. Here are some key steps to consider during your selection process:
1. Evaluating Their Portfolio
Review the past projects of potential mould makers. Look for:
- Diversity in products – Can they cater to different industries?
- Complex projects that showcase their problem-solving capabilities.
- Client testimonials and case studies demonstrating success.
2. Communication and Collaboration
A successful partnership hinges on clear communication. Ensure that your chosen injection mould maker:
- Is responsive to your inquiries.
- Offers collaboration throughout the design and manufacturing process.
- Values your input and adjusts accordingly.
3. After-Sales Support
The relationship doesn't end once the mould is delivered. Consider how well they support you post-delivery. Look for:
- Training on mould operation and maintenance.
- Technical support for troubleshooting any issues.
- Options for repairs or redesigns if necessary.
The Future of Injection Mould Making
The future of the mould-making industry is poised for transformation. With the increasing push towards sustainable manufacturing, the role of an injection mould maker will evolve to meet new demands:
1. Sustainability Initiatives
As businesses embrace eco-friendly practices, mould makers will need to consider:
- Using recyclable or biodegradable materials.
- Designing moulds that minimize waste.
- Implementing energy-efficient processes.
2. Industry 4.0 and Smart Manufacturing
The integration of IoT (Internet of Things), AI (Artificial Intelligence), and machine learning into manufacturing will revolutionize the way injection mould makers design and produce. Potential advancements include:
- Predictive maintenance for equipment.
- Real-time monitoring of production processes.
- Enhanced data analytics for continuous improvement.
Conclusion
In summary, the role of an injection mould maker is critical in ensuring quality, efficiency, and innovation in the manufacturing process. By selecting the right partner, such as those at hanking-mould.com, your business can leverage advanced capabilities to optimize production and thrive in today’s marketplace. Prioritize quality, communication, and adaptability to ensure your manufacturing processes remain on the cutting edge of technology and quality.
Investing in a skilled injection mould maker today guarantees that your products not only meet market demands but also position your business for future success.